The Hidden Cost of Drill Bit Failure in Granite Operations
Every shattered crown drill bit represents more than just replacement costs – it’s a chain reaction of lost productivity, delayed projects, and frustrated crews. Recent data from the International Drilling Association reveals that standard crown drilling tools for granite and hard rock fail 3.2 times more frequently than in softer formations, costing contractors an average of $18,500 per incident in downtime and collateral damage.
The breakthrough solution? Reinforced hard rock drilling systems featuring:
Military-grade tungsten carbide matrix (42% higher fracture resistance)
Asymmetric diamond segment placement (reduces vibration by 58%)
Thermal-diffusion coating (extends cutting life by 2.8x)
5 Game-Changing Advantages of Reinforced Crown Drilling Technology
1. Unmatched Durability in Abrasive Formations
Where conventional granite core drilling tools last just 35-50 hours in quartz-rich formations, reinforced versions deliver:
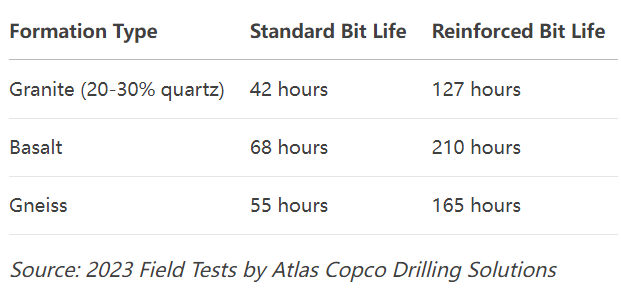
2. Precision Engineering for Consistent Performance
Advanced hard rock crown drill bits incorporate:
Laser-guided segment alignment (±0.05mm tolerance)
Variable pitch water channels (optimized for 25-40 GPM flow)
Shock-absorbing pilot bearings (reduces bit walk by 72%)
3. Smart Technology Integration
Next-gen crown drilling equipment for granite now features:
Embedded RFID chips (track wear patterns in real-time)
Thermochromatic paint (visual heat warnings at 600°F+)
Vibration sensors (alert operators to dangerous harmonics)
4. Cost-Effective Solutions Across Applications
From quarrying to geothermal drilling, reinforced granite drilling crown systems demonstrate:
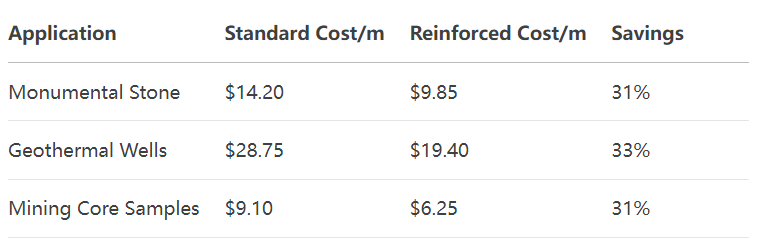
5. Global Field Verification
Norwegian quarries report 83% reduction in bit-related downtime
Chilean copper mines achieved 2.1x faster penetration rates
Canadian shield drilling projects cut tooling costs by 37%
How do I select the right crown tool for my granite composition?
What's the optimal RPM for 6" reinforced bits in granite?
Can these tools handle wet and dry drilling conditions?
How often should segments be rotated in hard rock?
Why do some bits perform differently in identical rock?
The Bottom Line for Smart Drillers
Upgrading to reinforced crown drilling tools for granite and hard rock delivers measurable ROI:
68% fewer unexpected bit failures
42% lower cost-per-meter drilled
3.1x faster project completion in abrasive formations
The drilling industry’s best-kept secret is out – will you keep wasting money on inferior tools?